Di pîşesaziya granulasyonê de, çi makîneya peletê ya qalibê deşt be, çi jî makîneya peletê ya qalibê zengil be, prensîba xebata wê ew e ku li ser tevgera nisbî ya di navbera qalibê zextê û qalibê de bisekine da ku materyalê bigire û bikeve stasyona bi bandor, wê derxîne şeklê xwe, û dûv re bi kêra birrînê wê bike perçeyên bi dirêjahiya pêwîst.
Qalika rolika çapa perçeyan
Qalikê rolika zextê bi giranî ji mîlek eksentrîk, belîngirên gêrîk, qalikek rolika zextê ya li derveyî mîla rolika zextê ya li ser milên wê, û pêkhateyên ku ji bo piştgirî û rastkirina qalika rolika zextê têne bikar anîn pêk tê.
Qalika çerxa zextê materyalê dixe nav qulika qalibê û di bin zextê de di qulika qalibê de çêdike. Ji bo ku çerxa zextê neqelişe û hêza girtinê zêde bibe, divê di navbera çerxa zextê û materyalê de hêzek xişandinê ya diyarkirî hebe. Ji ber vê yekê, tedbîrên ji bo zêdekirina xişandin û berxwedana li hember aşînê pir caran li ser rûyê çerxa zextê têne girtin. Dema ku parametreyên avahîsaziyê yên çerxa zextê û qalibê têne destnîşankirin, şiklê avahîsaziyê û mezinahiya rûyê derve yê çerxa zextê bandorek girîng li ser karîgeriya granulasyonê û kalîteya perçeyan dike.
Pêkhateya rûyê qalikê rollera zextê
Sê cureyên rûyên hevpar ji bo silindirên presa perçeyan ên heyî hene: rûyê silindirê xêzkirî, rûyê silindirê xêzkirî bi mohra qiraxê, û rûyê silindirê şaneyekê.
Gulera zextê ya cureyê xelekên dirandî xwedî performansa gerandina baş e û bi berfirehî di kargehên xwarina ajalan û mirîşkan de tê bikar anîn. Lêbelê, ji ber xitimîna xwarinê di xelekên dirandî de, lixwekirina gulera zextê û qalibê zengilî ne pir yekreng e, û li her du serên gulera zextê û qalibê zengilî lixwekirin girantir e.
Çerxa zextê ya cureyê xelekên dirandî bi mohra qiraxan bi piranî ji bo hilberîna materyalên avî guncaw e. Materyalên avî di dema derxistinê de bêtir meyla şemitandinê dikin. Ji ber mohra qiraxan li her du aliyên xelekên dirandî, di dema derxistina xwarinê de şemitandina ber bi her du aliyan ve ne hêsan e, di encamê de belavkirina xwarinê yekrengtir dibe. Lixwekirina çelekên zextê û qalibê zengilî jî yekrengtir dibe, di encamê de dirêjahiya peletên hilberandî yekrengtir dibe.
Sûdê rolika şaneyê hingiv ew e ku lixwekirina qalibê zengilî yekreng e, û dirêjahiya perçeyên hilberandî jî nisbeten yekreng e. Lêbelê, performansa bobînê nebaş e, ku bandorê li derana granulatorê dike û ne bi qasî karanîna celebê slotê di hilberîna rastîn de gelemper e.
Ev a jêrîn kurteyek ji 10 cureyên silindirên zextê yên makîneya perçeyan ji bo qalibên zengilên silindirên zextê yên Baoshell e, û 3 yên dawîn bê guman ew in ku we nedîtine!
Cureyê xêzikê NO.10
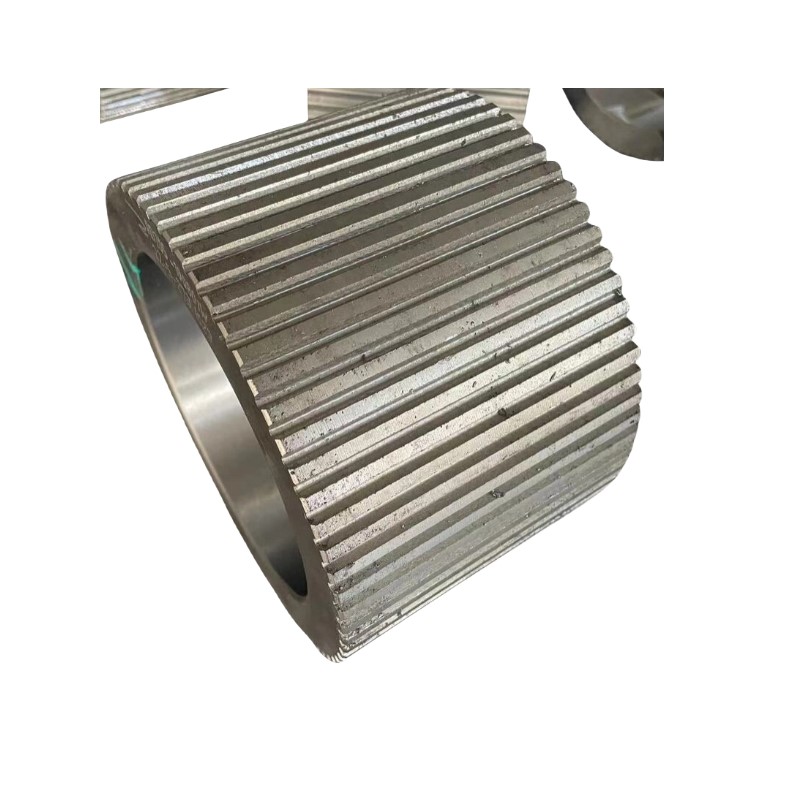
NO.9 Cureyê lûleya girtî
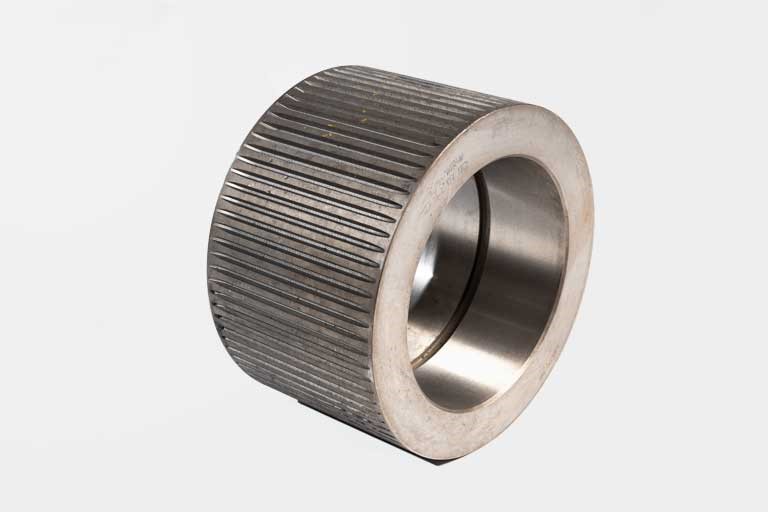
NO.8 Cureyê şaneya hingiv
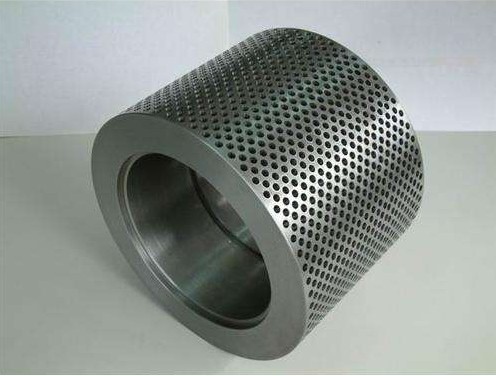
NO.7 Bi şiklê elmasê
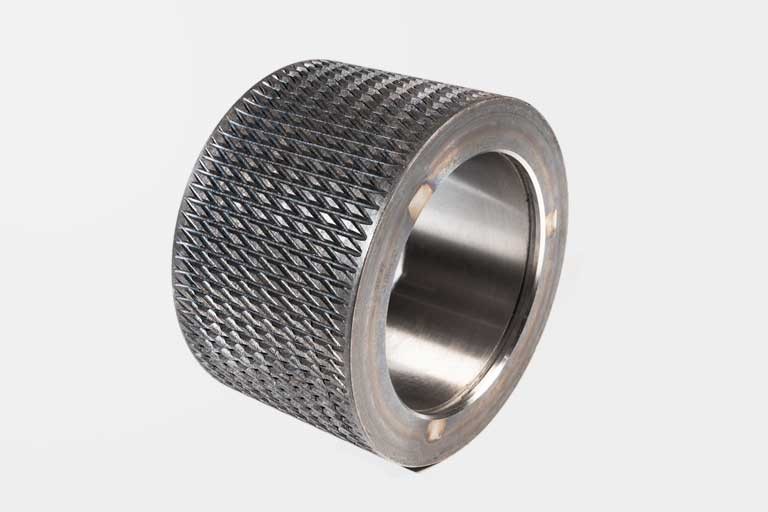
NO.6 Xêza meyldar
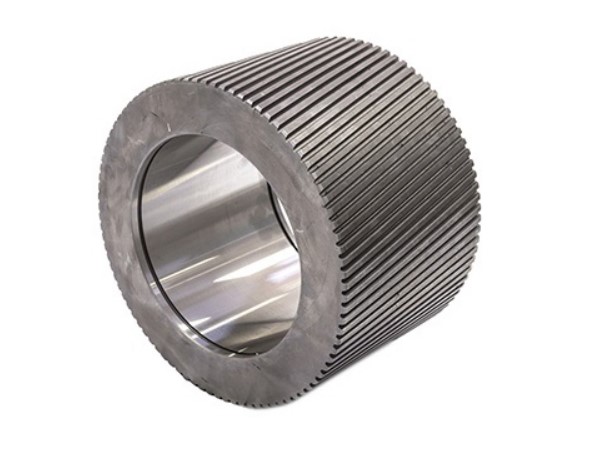
NO.5 Groove+hingiv
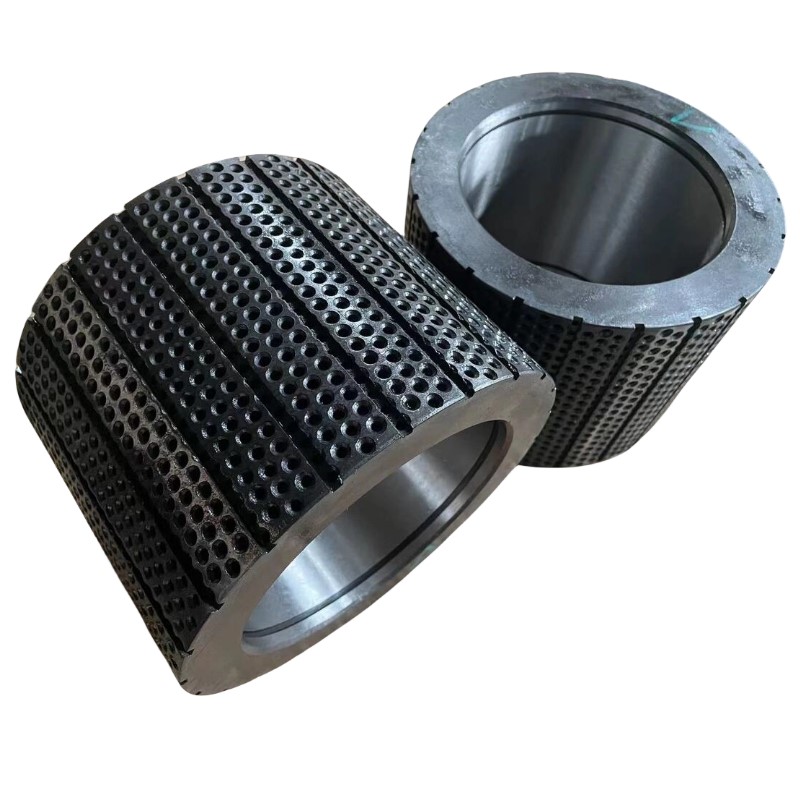
NO.4 Xêzika girtî + şane
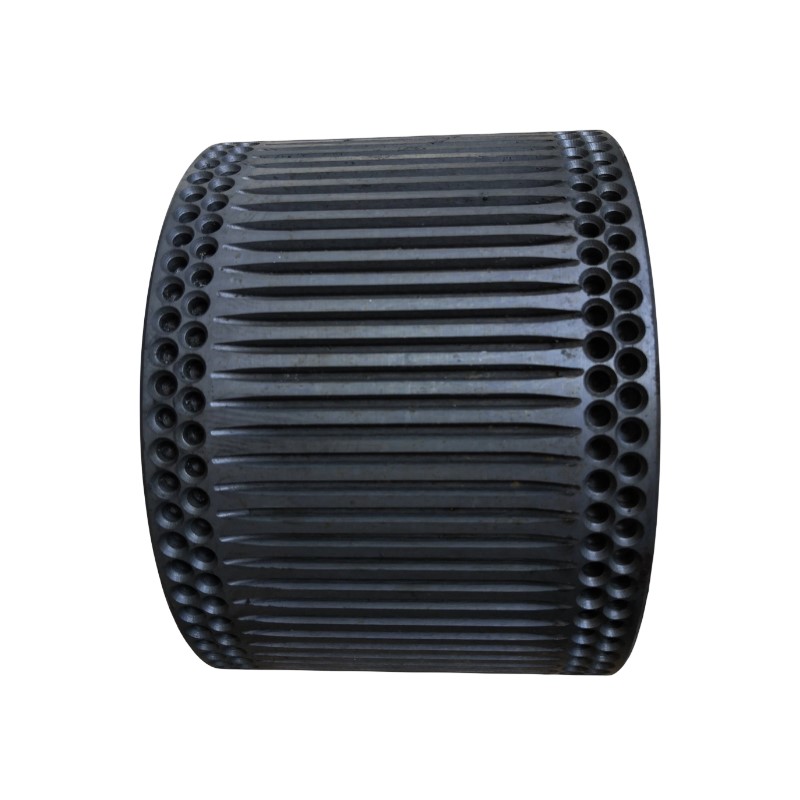
NO.3 Xêzika meyldar + şane
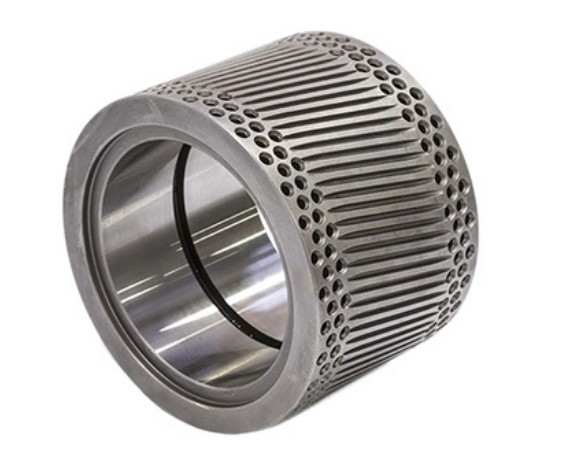
NO.2 Pêlbûna hestiyê masî
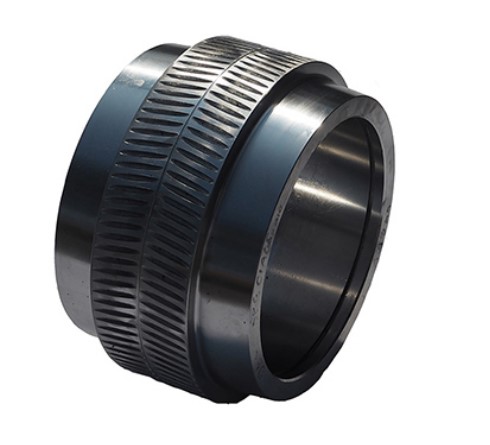
NO.1 Pêlên bi şiklê kevanê
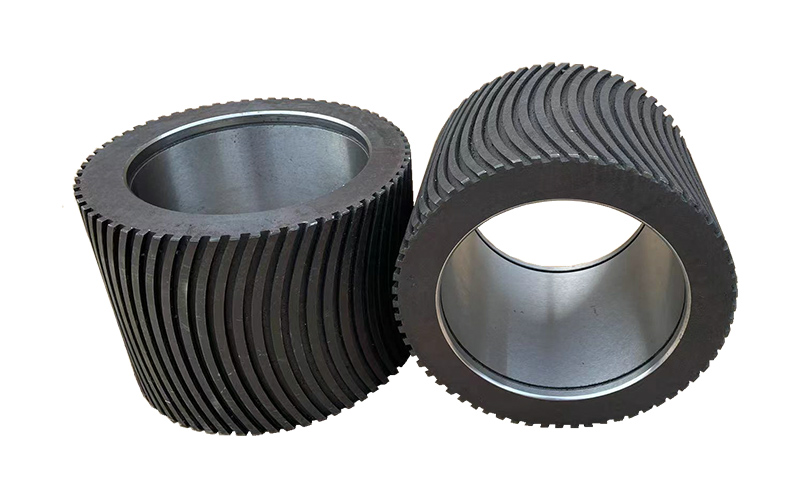
MODELA TAYBET: QALIKA KOLERA TUNGSTEN KARBÎD
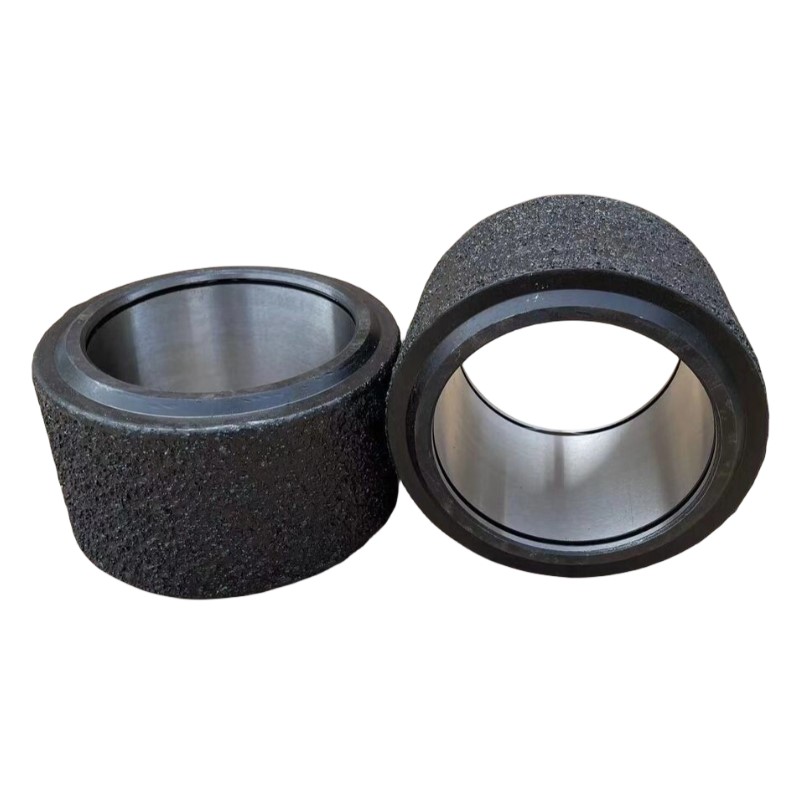
Rêbaza dermankirinê ji bo şemitîna rolika zextê ya makîneya perçeyan
Ji ber jîngeha xebatê ya dijwar, şiddeta xebatê ya bilind, û rêjeya zû ya lixwekirinê ya qalikê çerxa zextê, çerxa zextê beşek hesas a makîneya perçeyan e û pêdivî ye ku bi rêkûpêk were guhertin. Pratîka hilberînê nîşan daye ku heya ku taybetmendiyên materyalên hilberînê biguherin an jî şert û mercên din di dema pêvajoyê de biguherin, dibe ku diyardeya şemitîna çerxa zextê ya makîneya perçeyan çêbibe. Ger di dema pêvajoya granulasyonê de şemitîna çerxa zextê hebe, ji kerema xwe netirsin. Ji bo hûrguliyên taybetî, ji kerema xwe li teknîkên jêrîn binêrin:
Sedem 1: Sazkirina kêm a çerxa zextê û mîlê
Çare:
Ji bo ku qalikê rolera zextê ber bi aliyekî ve neçe, kontrol bikin ka sazkirina beringên ruloya zextê maqûl e an na.
Sedem 2: Devê zengilê qalibê zengilê rast hatiye hûrkirin, ji ber vê yekê qalib materyalan naxwe.
Çare:
Lixwebûna kelepçeyan, tekerên veguheztinê û zengilên astarê yên granulatorê kontrol bikin.
Asta sazkirina qalibê zengilê bi awayekî hevseng rast bikin, bi xeletiyek ku ji 0.3 mm zêdetir nebe.
Divê valahiya di navbera silindirên zextê de wiha were sererastkirin: nîvê rûyê xebatê yê silindirên zextê bi qalibê re dixebite, û divê çerxa verastkirina valahiyê û pêça kilîtkirinê jî di rewşa xebatê ya baş de bin.
Dema ku silindira zextê diqelişe, nehêlin makîneya perçeyan demek dirêj bêkar bimîne û li bendê bin ku ew bi tena serê xwe materyalê derxe.
Rêjeya zextkirinê ya vebûna qalibê zengilî ya ku tê bikar anîn pir zêde ye, ku ev yek dibe sedema berxwedana bilind a derxistina materyalê ya qalibê û her weha yek ji sedemên şemitîna rolika zextê ye.
Divê destûr neyê dayîn ku makîneya peletê bêyî xwarina materyalê bêsedem bêkar bimîne.
Sedem 3: Hilgirtina zextê asê maye
Çare:
Bearingên rollerên zextê biguherînin.
Sedem 4: Qalika çerxa zextê ne gilover e
Çare:
Kalîteya qalikê silindir bêkalîte ye, qalikê silindir biguherînin an tamîr bikin.
Dema ku çarika zextê diqelişe, divê di wextê xwe de were rawestandin da ku ji xişandina bêkar a dirêj a çarika zextê dûr bikeve.
Sedem 5: Çemandin an sistkirina milê çerxa zextê
Çare:
Dema ku qalibê zengil û rolera zextê diguherînin, milê biguherîne an teng bike, û rewşa milê tekerê zextê kontrol bike.
Sedem 6: Rûyê xebatê yê çerxa zextê bi nisbeten nelihevhatî bi rûyê xebatê yê qalibê zengilê re ye (derbasbûna qiraxan)
Çare:
Kontrol bikin ka rolika zextê bi şaşî hatiye sazkirin û wê biguherînin.
Kontrol bike ka şafta eksentrîk a silindira zextê deform bûye an na.
Li ser bearingên şaftê sereke an jî bushingên makîneya perçeyan xisarê kontrol bike.
Sedem 7: Paqijiya milê granulatorê pir mezin e
Çare:
Valahiya tengbûna granulatorê kontrol bikin.
Sedem 8: Rêjeya qulkirina qalibê zengilê kêm e (kêmtir ji 98%)
Çare:
Ji bo ku qulika qalibê bi makîneyeke pistolê bikolin, an jî di rûn de bikelînin, berî xwarinê biçirînin.
Sedem 9: Madeyên xav pir qalind in û rêjeya şilbûna wan zêde ye
Çare:
Bala xwe bidinê ku rêjeya şilbûnê di dora %15 de bimîne. Ger rêjeya şilbûna madeyên xav pir zêde be, piştî ku madeyên xav dikevin nav qalibê zengilî, dê qalib asteng bibe û şemite. Rêzeya kontrola şilbûna madeyên xav di navbera %13-20 de ye.
Sedem 10: Qaliba nû pir zû dixwe
Çare:
Leza xwe rast bikin da ku pê ewle bibin ku kişana pêça zextê têr e, pêşî li şemitîna pêça zextê bigirin, û di cih de lixwekirina qalibê zengilê û pêça zextê kontrol bikin.
Dema weşandinê: 25ê Adarê, 2024